Nissan Rogue Service Manual: Periodic maintenance
HEADLAMP AIMING ADJUSTMENT
Inspection
PREPARATION BEFORE ADJUSTING
Before performing aiming adjustment, check the following:
NOTE:
- For headlamp aiming details, refer to regulations in your area.
- By regulation, no means for horizontal aim adjustment is provided
from the factory; only vertical aim is
adjustable.
- Use adjusting screw to perform aiming adjustment.
- Perform headlamp aiming if:
- The vehicle front body has been repaired;
- The front combination lamp has been removed or replaced;
- Any outfitting has been installed;
- The vehicle’s standard load condition has been substantially
increased.
AIMING ADJUSTMENT SCREW
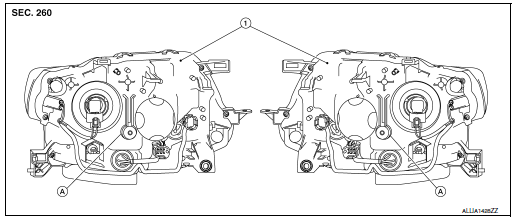
- Front combination lamp
(view from rear)
- Headlamp HI/LO (UP/DOWN)
adjustment screw
Aiming Adjustment Procedure
Aiming Chart
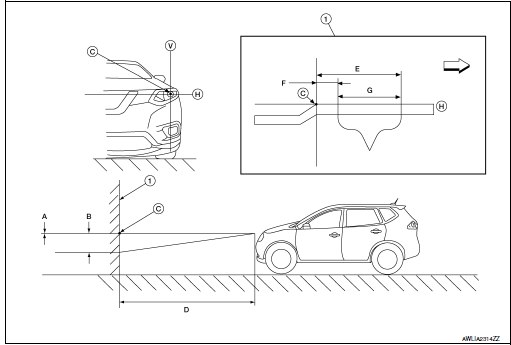
- Adjustment screen
- Highest cutoff line height
- Lowest cutoff line height
- Headlamp bulb center (H-V point)
- Distance of headlamp aiming
screen from vehicle 7.62 m (25 ft)
- Maximum aim evaluation distance
from vertical center on aiming
screen 399 mm (3°R)
- Minimum aim evaluation distance
from vertical center on aiming
screen 133 mm (1°R)
- Aim evaluation area H. Horizontal aiming evaluation line
- Vertical aiming evaluation line
Right
A (Highest cutoff line height) -13.3 mm (0.5 in) 0.1° up
B (Lowest cutoff line height) 53.2 mm (2.1 in) 0.4° down
LOW BEAM AND HIGH BEAM
NOTE:
- Basic illuminating area for evaluation and/or adjustment should be
within range shown on aiming chart.
- Use adjustment screw to perform aiming adjustment.
- Ensure fog lamps are turned off.
- Block the opposite headlamp from projecting a beam pattern onto the
adjustment screen, using a suitable
object. Aim each headlamp individually.
CAUTION:
Do not cover the lens surface with a tape etc. The lens is made of resin.
- Place the screen on the same level and flat surface as the vehicle.
NOTE:
Surface should be free of any debris that would cause a difference between
the headlamp center and the
adjustment screen.
- Face the front of the vehicle to the screen and measure distance
between the headlamp center and the
screen surface.
Distance between the headlamp center and the screen (D) : 7.62 m (25 ft)
- Start the engine. Turn the headlamp on.
- Determine the preferred vertical aim range dimensions, using the aiming
chart.
- Measure the projected beam within the aim evaluation segment on the
screen.
- Adjust the beam pattern of each headlamp until the aim evaluation
segment (the area relative to both the
highest and lowest cutoff line height) is positioned within the vertical aim
range dimensions shown on the
aiming chart.
FRONT FOG LAMP AIMING ADJUSTMENT
Aiming Adjustment Procedure
Aiming Chart
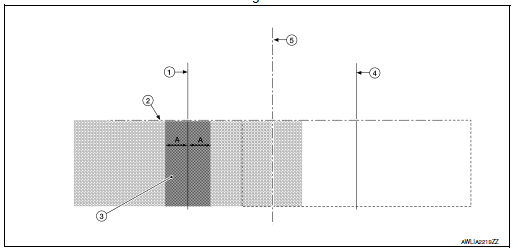
- Vertical center line of fog lamp
(LH)
- Lamp center above ground
- Fog lamp high intensity area
(LH)
- Vertical center line of fog lamp
(RH)
- Vertical center axis
- 100mm (4in)
NOTE:
- (LH) Fog lamp aiming specifications shown, (RH) similar.
- Check the following conditions before performing the aiming
adjustment.
- Keep all tires inflated to correct pressure.
- Place vehicle on level ground.
- See that vehicle is unloaded (except for full levels of coolant,
engine oil and fuel, and spare tire, jack, and
tools). Have the driver or equivalent weight placed in driver seat.
- When performing adjustment, if necessary, cover the headlamps and
opposite fog lamp.
- Set the distance between the screen and the center of the fog
lamp lens as shown.
(1) Aiming screen or a matte white surface
(2) 7.62 m (25 ft)
(3) Floor to center of fog lamp lens
(4) Floor
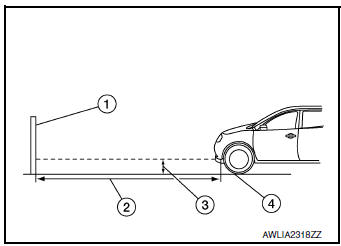
- Turn front fog lamps ON.
- Access adjusting screw (A) from underneath front bumper fascia.
Adjust front fog lamps using adjusting screw so that the top
edge of the high intensity zone is at the fog lamp centers above
ground.
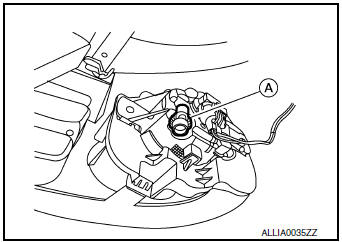
EXTERIOR LIGHTING SYSTEM SYMPTOMS
Symptom Table
CAUTION:
Perform the self-diagnosis with CONSULT before the symptom diagnosis. Perform
the trouble diagnosis
if any DTC is detected.
NORM ...
FRONT COMBINATION LAMP
Exploded View
Front fender
Front combination lamp
Clip
Removal and Installation
REMOVAL
Remove front bumper fascia. Refer to EXT-17, "Removal an ...
Other materials:
System description
COMPONENT PARTS
POWER DOOR LOCK SYSTEM
POWER DOOR LOCK SYSTEM : Component Parts Location
No
Component
Function
1
BCM
Controls the door lock system.
Refer to BCS-79, "BODY CONTROL SYSTEM : Component Parts Location" for
detailed
instal ...
P1574 ASCD vehicle speed sensor
Description
The ECM receives two vehicle speed sensor signals via CAN communication line.
One is sent from combination
meter, and the other is from TCM (Transmission control module). The ECM uses
these signals for ASCD
control. Refer to EC-47, "AUTOMATIC SPEED CONTROL DEVICE (ASCD) : Sys ...
LATCH (Lower Anchors and Tethers for CHildren) System
LATCH system lower anchor locations - bench seat
Your vehicle is equipped with special anchor
points that are used with LATCH system compatible
child restraints. This system may also be
referred to as the ISOFIX or ISOFIX compatible
system. With this system, you do not have to use
a vehicl ...
© 2014-2025 Copyright www.nirogue.com