Nissan Rogue Service Manual: Unit disassembly and assembly
ELECTRIC CONTROLLED COUPLING
Exploded View
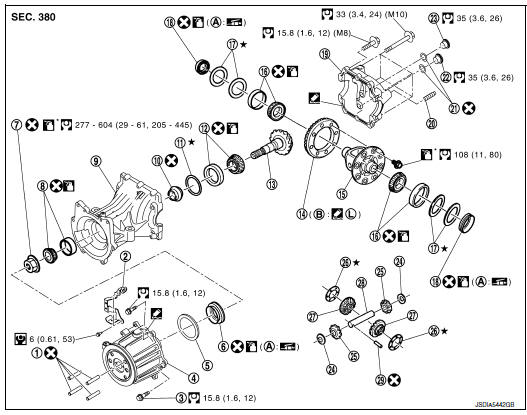
- Stud bolt
- Connector bracket
- Reamer bolt
- Electric controlled coupling assembly
- Wave spring
- Drive pinion oil seal
- Drive pinion lock nut
- Pinion front bearing
- Gear carrier
- Collapsible spacer
- Drive pinion adjusting shim
- Pinion rear bearing
- Drive pinion
- Drive gear
- Differential case
- Side bearing
- Side bearing adjusting shim
- Side oil seal
- Rear cover
- Stud bolt
- Gasket
- Drain plug
- Filler plug
- Pinion mate thrust washer
- Pinion mate gear
- Side gear thrust washer
- Side gear
- Pinion mate shaft
- Lock pin
- Oil seal lip
- Screw hole
: N·m (kg-m, in-lb)
: N·m (kg-m, ft-lb)
: Always replace after every
disassembly.
: Select with proper thickness.
: Apply gear oil.
*: Apply anti-corrosion oil.
: Apply multi purpose grease.
: Apply Genuine Silicone RTV or
equivalent. Refer to GI-22, "Recommended Chemical Products and Sealants".
: Apply Genuine High Strength
Thread Locking Sealant or equivalent. Refer to GI-22, "Recommended Chemical
Products
and Sealants".
Disassembly and Assembly
DISASSEMBLY
- Remove stud bolts .
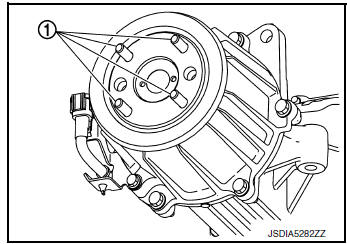
- Remove electric controlled coupling assembly from final drive
assembly.
- Remove wave spring.
- Remove drive pinion oil seal from the inside of gear carrier.
Refer to DLN-136, "Disassembly and Assembly".
CAUTION:
When removing electric controlled coupling, replace drive
pinion oil seal.
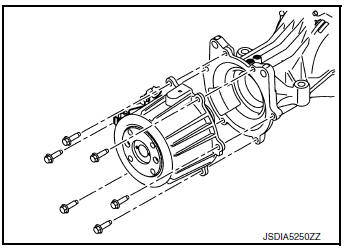
- Remove connector bracket 1 from electric controlled coupling.
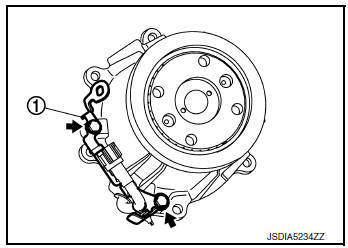
- Separate band clip and connector clip from connector bracket.
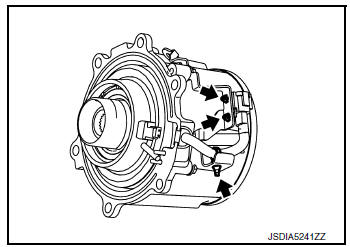
ASSEMBLY
- Install connector bracket to electric controlled coupling.
- For tightening torque, refer to DLN-120, "Exploded View".
- Fix AWD solenoid harness with band clip and connector clip.
- Install drive pinion oil seal to the inside of gear carrier. Refer
to
DLN-136, "Disassembly and Assembly".
CAUTION:
When removing electric controlled coupling, replace drive
pinion oil seal.
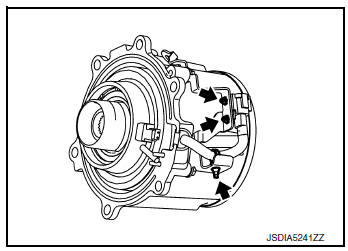
- Install wave spring 1 to the inside of gear carrier.
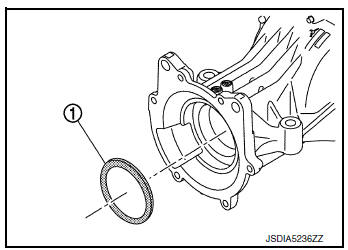
- Apply liquid gasket to mating surface of electric controlled coupling
assembly.
CAUTION:
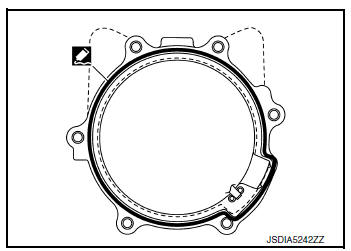
- Match electric controlled coupling assembly 1 to spline of drive
pinion, then install it to final drive assembly 2.
CAUTION:
Be careful not to damage drive pinion oil seal.
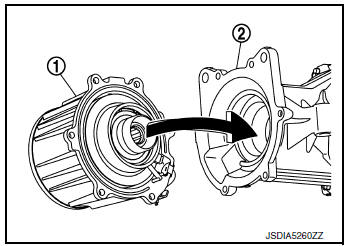
- Temporarily tighten reamer bolts 1 to the positions shown in the
figure.
- Tighten reamer bolts and electric controlled coupling assembly
mounting bolts to the specified torque.
- For tightening torque, refer to DLN-120, "Exploded View".
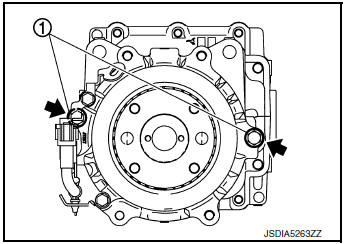
- Install stud bolts 1.
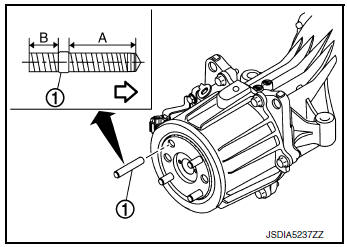
: Electric controlled
coupling side
Thread length
A : Long
B : Short
CAUTION:
- Never reuse stud bolt.
- Screw long thread side of stud bolt to electric controlled
coupling.
- Screw the stud bolt until the stop by applying a torque of 15
N·m (1.5 kg-m, 11 ft-lb) ±20%.
- After installing stud bolt, the length of the protrusion from
electric controlled coupling must be
19.8 mm (0.780 in) ±1.4 mm (0.055 in).
DIFFERENTIAL ASSEMBLY
Exploded View
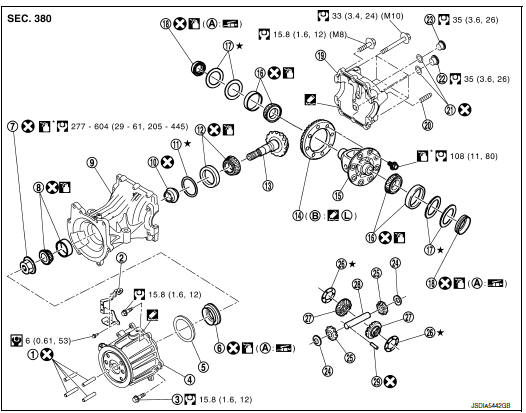
- Stud bolt
- Connector bracket
- Reamer bolt
- Electric controlled coupling assembly
- Wave spring
- Drive pinion oil seal
- Drive pinion lock nut
- Pinion front bearing
- Gear carrier
- Collapsible spacer
- Drive pinion adjusting shim
- Pinion rear bearing
- Drive pinion
- Drive gear
- Differential case
- Side bearing
- Side bearing adjusting shim
- Side oil seal
- Rear cover
- Stud bolt
- Gasket
- Drain plug
- Filler plug
- Pinion mate thrust washer
- Pinion mate gear
- Side gear thrust washer
- Side gear
- Pinion mate shaft
- Lock pin
- Oil seal lip
- Screw hole
: N·m (kg-m, in-lb)
: N·m (kg-m, ft-lb)
: Always replace after every
disassembly.
: Select with proper thickness.
: Apply gear oil.
*: Apply anti-corrosion oil.
: Apply multi purpose grease.
Apply Genuine Silicone RTV or
equivalent. Refer to GI-22, "Recommended Chemical Products and Sealants".
: Apply Genuine High Strength
Thread Locking Sealant or equivalent. Refer to GI-22, "Recommended Chemical
Products
Disassembly and Assembly
DISASSEMBLY
- Remove drain plug, filler plug and gaskets.
- Remove the side oil seal, using oil seal remover (commercial
service tool).
CAUTION:
Never damage gear carrier and rear cover.
- Remove rear cover mounting bolts.
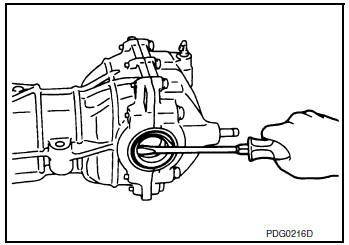
- Set drifts (A and B) to the right and left side bearing adjusting
shims individually. Press differential assembly with side bearing
to remove gear carrier assembly and rear cover assembly.
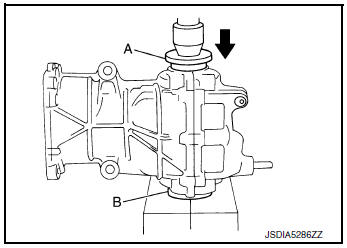
A : Drift [SST: KV40100610 (J-26089)]
B : Drift [SST: KV40100610 (J-26089)]
CAUTION:
The pressure shall be as low as possible to remove gear
carrier assembly and rear cover assembly. The maximum
pressure shall be 10 kN (1 ton, 1.0 Imp ton).
NOTE:
Differential assembly, side bearings, and adjusting washers are
compressed and integrated in gear carrier and rear cover.
- Remove stud bolt from rear cover.
NOTE:
It is not necessary to remove stud bolt except when it is replaced.
- Remove side bearing adjusting shims and side bearing outer races.
CAUTION:
Mark the side bearing adjusting shims so that the original mounting
positions (right/left) can be
identified later.
- Remove side bearing inner races, using adaptor (A), separator
(B) and puller (C).
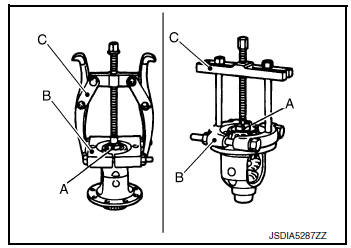
A : Adaptor [ST33052000 ( — )]
B : Separator (commercial service tool)
C : Puller (commercial service tool)
CAUTION:
- To prevent damage to the side bearing and drive gear,
place copper plates between these parts and vise.
- It is not necessary to remove side bearing inner race
except when it is replaced.
- For proper reinstallation, paint matching marks A on one differential
assembly and drive gear.
CAUTION:
For matching marks, use paint. Never damage differential
assembly and drive gear.
- Remove drive gear mounting bolts and then remove drive gear
from differential assembly.
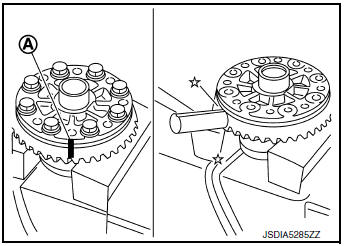
- Remove lock pin of pinion mate shaft, using the pin punch (commercial
service tool).
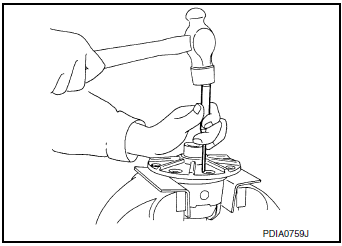
- Remove pinion mate shaft.
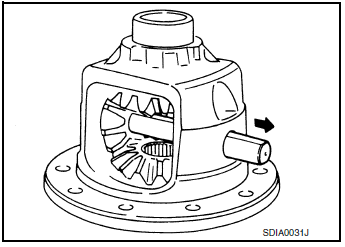
- Remove pinion mate gears, pinion mate thrust washers, side
gears, side gear thrust washers from differential case.
- Perform inspection after disassembly. Refer to DLN-134,
"Inspection".
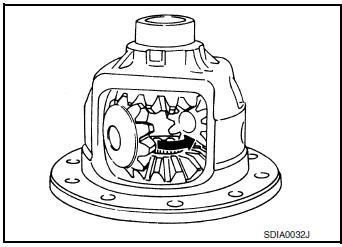
ASSEMBLY
- Install side gear thrust washers with the same thickness as the
ones installed prior to disassembly or reinstall the old ones on
the side gears.
- Install side gears and side gear thrust washers into differential
case.
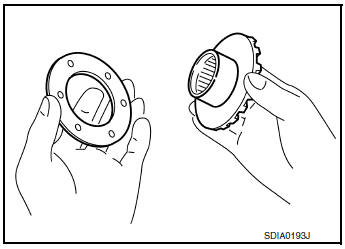
- Align 2 pinion mate gears in diagonally opposite positions, then
rotate and install them into differential case after installing thrust
washer to pinion mate gear.
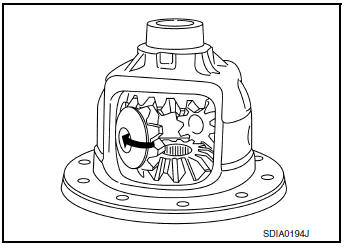
- Align the lock pin holes on differential case with pinion mate
shaft, and install pinion mate shaft.
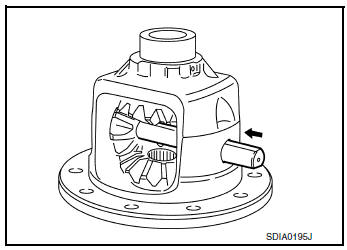
- Measure side gear end play. If necessary, select the appropriate side
gear thrust washers.
- Place differential assembly straight up so that side gear to be
measured comes upward.
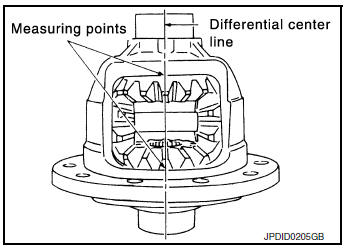
- Using feeler gauge, measure the clearance between side gear
back and differential case at 3 different points, while rotating
side gear. Average the 3 readings, and then measure the clearance
of the other side as well.
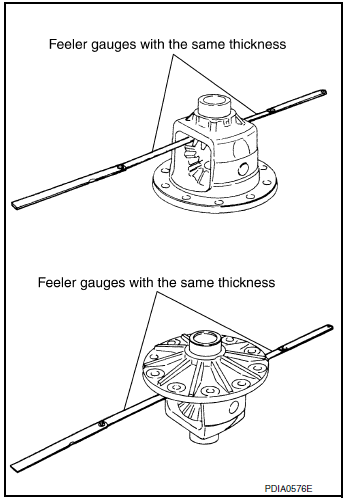
Side gear back clearance
: Refer to DLN-141, "Differential
Side Gear Clearance".
CAUTION:
To prevent side gear from tilting, insert feeler gauges with
the same thickness from both sides.
- If the back clearance is outside the specification, use a thicker/
thinner side gear thrust washer to adjust. For selecting thrust
washer, refer to the latest parts information.
When the back clearance
is large
: Use a thicker thrust washer.
When the back clearance
is small: Use a thinner thrust washer.
CAUTION:
Select a side gear thrust washer for right and left individually.
- Drive a lock pin into pinion mate shaft, using the pin punch
(commercial service tool).
CAUTION:
Never reuse lock pin.
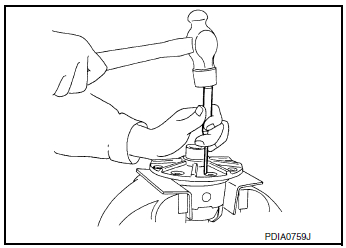
- Press side bearing inner races to differential assembly, using the
drifts (A and B).
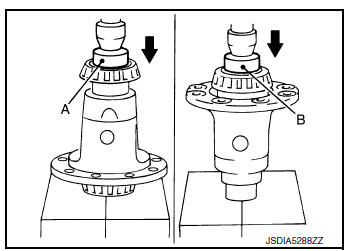
A : Drift [SST: KV40105020 ( — )]
B : Drift [SST: KV40105020 ( — )]
CAUTION:
- Never reuse side bearing inner race.
- Apply gear oil to side bearing.
- Apply thread locking sealant into the thread hole of drive gear.
CAUTION:
Clean and degrees drive gear back and threaded holes sufficiently.
- Install the drive gear to differential assembly.
CAUTION:
Align the matching mark of differential assembly and drive
gear.
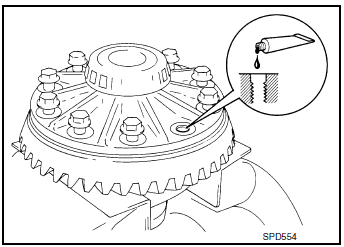
- Tighten the bolts in a crisscross fashion to the specified torque.
- For tightening torque, refer to DLN-124, "Exploded View".
CAUTION:
Apply anti-corrosion oil to the thread and seat of mounting
bolts.
- Assemble side bearing outer races to inner races.
CAUTION:
- Never reuse side bearing outer race.
- Apply gear oil to side bearing.
- Install new side bearing adjusting shims (2 pieces for one side)
with the same thickness as the ones installed prior to disassembly
or re-install the old ones, on side bearing outer race of differential
assembly.
If side bearing adjusting shims have been already selected, use them.
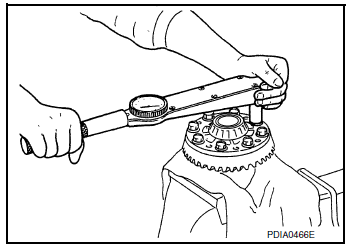
- Set the drifts (A and B) to the right and left side bearing adjusting
shims individually. Compress differential assembly and side
bearing to gear carrier assembly to install differential assembly.
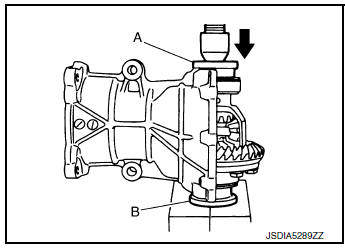
A : Drift [KV40100610 (J-26089)]
B : Drift [KV40100610 (J-26089)]
CAUTION:
- The drift shall be placed on the center of the adjusting
shims.
- The pressure shall be as low as possible to install
differential
assembly into gear carrier assembly. The maximum
pressure shall be 10 kN (1 ton, 1.1 US ton, 1.0 Imp ton).
- If the adjusting shims are installed by tapping, the gear
carrier may be damaged. Avoid tapping.
- Install dummy cover set [SST: KV381086S1 ( — )], check and adjust
drive gear runout, tooth contact,
backlash, and total preload torque. Refer to DLN-130, "Adjustment".
- Remove dummy cover set.
- Install stud bolt to rear cover.
CAUTION:
Screw the stud bolt until the thread becomes invisible by applying a torque
of 20 N·m (2.0 kg-m, 15
ft-lb) or less.
- Apply liquid gasket to mating surface of rear cover.
CAUTION:
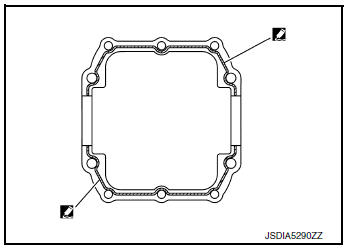
- Set the drifts (A and B) to the right and left side bearing adjusting
shims individually. Compress differential assembly and side
bearing to install rear cover.
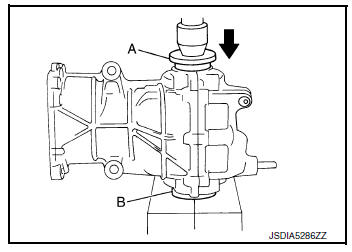
A : Drift [KV40100610 (J-26089)]
B : Drift [KV40100610 (J-26089)]
CAUTION:
- Tighten rear cover mounting bolts to the specified torque.
- For tightening torque, refer to DLN-124, "Exploded View".
- Using the drift (A) [SST: KV38100200 (J-26233)], drive side oil
seals until it becomes flush with the gear carrier end.
CAUTION:
- Never reuse oil seals.
- When installing, do not incline oil seals.
- Apply multi-purpose grease onto oil seal lips, and gear oil
onto the circumference of oil seal.
- Check total preload torque. Refer to DLN-130, "Adjustment".
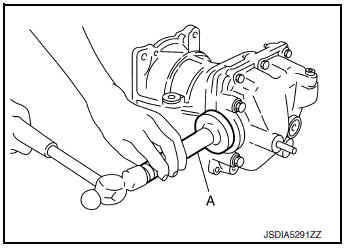
Adjustment
TOTAL PRELOAD TORQUE
- Remove electric controlled coupling assembly. Refer to DLN-121,
"Disassembly and Assembly".
- Rotate drive pinion back and forth 2 to 3 times to check for
unusual noise and rotation malfunction.
- Rotate drive pinion at least 20 times to check for smooth operation
of the bearing.
- Fit drive pinion socket onto drive pinion spline. Measure the
total
preload, using the preload gauge and drive pinion socket.
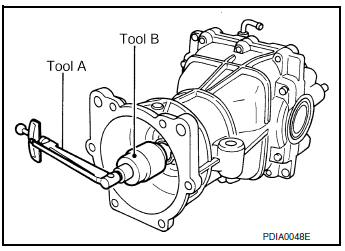
A : Preload gauge [SST: ST3127S000 (J-25765-A)]
B : Drive pinion socket [SST: KV38109500 ( — )]
Standard
Total preload torque : Refer to DLN-141, "Preload
Torque".
NOTE:
Total preload torque = Pinion bearing torque + Side bearing torque
When the preload torque is large
On pinion bearings: Replace the collapsible spacer.
On side bearings: Use thinner side bearing adjusting shims. For selecting
adjusting
shim, refer to the latest parts information.
When the preload is small
On pinion bearings: Tighten the drive pinion nut.
On side bearings: Use thicker side bearing adjusting shims. For selecting
adjusting
shim, refer to the latest parts information.
DRIVE GEAR RUNOUT
- Remove rear cover. Refer to DLN-125, "Disassembly and Assembly".
- Following the procedure below, install a dummy cover set [SST:
KV381086S1 ( — )] to gear carrier.
- Set dummy cover shims [SST: KV38108630 ( — )] to the right and left side
bearing adjusting
shims.
- Temporarily tighten dummy cover [SST: KV38108610 ( — )] to gear
carrier.
- Position dummy cover spacers [SST: KV38108621 ( — )] to dummy cover
[SST: KV38108610
( — )].
- Tighten rear cover mounting bolts to the specified torque. Refer
to DLN-124, "Exploded View".
- Tighten dummy cover spacer mounting bolts evenly to the specified
torque.
: 5.9 N·m (0.6 kg-m, 52
in-lb)
- Fit a dial indicator to the drive gear back face.
- Rotate the drive gear to measure runout.
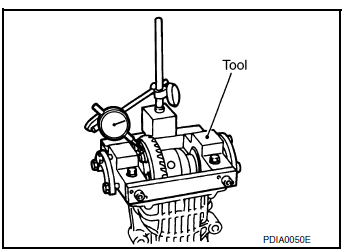
Limit
Drive gear back face
runout
: Refer to DLN-141, "Drive
Gear Runout".
- If the runout is outside of the repair limit, check drive gear
assembly condition; foreign material may be caught between
drive gear and differential case, or differential case or drive
gear may be deformed, etc.
CAUTION:
Replace drive gear and drive pinion as a set.
TOOTH CONTACT
- Remove rear cover. Refer to DLN-125, "Disassembly and Assembly".
- Following the procedure below, install a dummy cover set [SST:
KV381086S1 ( — )] to gear carrier.
- Set dummy cover shims [SST: KV38108630 ( — )] to the right and
left side bearing adjusting
shims.
- Temporarily tighten dummy cover [SST: KV38108610 ( — )] to gear
carrier.
- Position dummy cover spacers [SST: KV38108621 ( — )] to dummy
cover [SST: KV38108610
( — )].
- Tighten rear cover mounting bolts to the specified torque. Refer
to DLN-124, "Exploded View".
- Tighten dummy cover spacer mounting bolts evenly to the specified
torque.
: 5.9 N·m (0.6 kg-m, 52
in-lb)
- Apply red lead to drive gear.
CAUTION:
Apply red lead to both the faces of 3 to 4 gears at 4 locations
evenly spaced on drive gear.
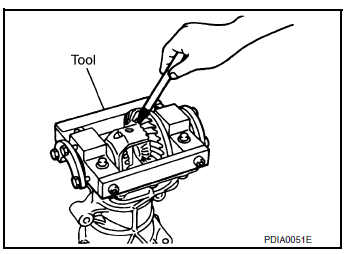
- Rotate drive gear back and forth several times, check drive pinion
gear to drive gear tooth contact.
CAUTION:
Check tooth contact on drive side and reverse side.
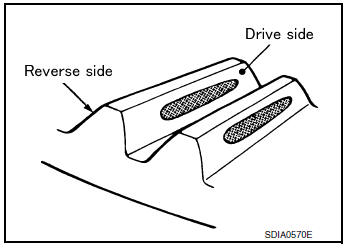
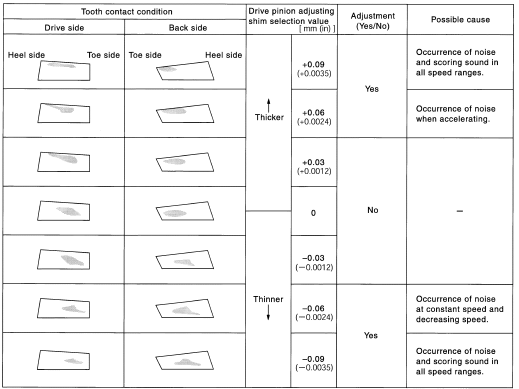
Tooth Contact Judgment Guide
- If tooth contact is improperly adjusted, follow the procedure
below to adjust the pinion height (dimension X).
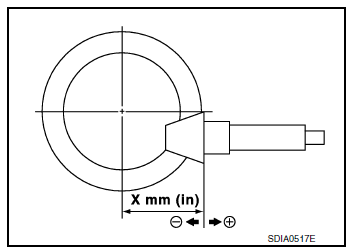
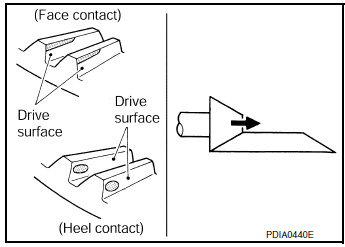
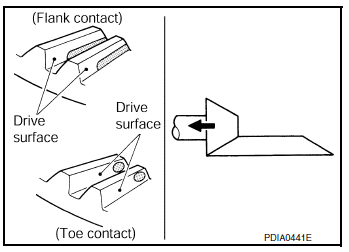
BACKLASH
- Remove rear cover. Refer to DLN-125, "Disassembly and Assembly".
- Following the procedure below, install a dummy cover set [SST:
KV381086S1 ( — )] to gear carrier.
- Set dummy cover shims [SST: KV38108630 ( — )] to the right and
left side bearing adjusting
shims.
- Temporarily tighten dummy cover [SST: KV38108610 ( — )] to gear
carrier.
- Position dummy cover spacers [SST: KV38108621 ( — )] to dummy
cover [SST: KV38108610
( — )].
- Tighten rear cover mounting bolts to the specified torque. Refer
to DLN-124, "Exploded View".
- Tighten dummy cover spacer mounting bolts evenly to the specified
torque.
: 5.9 N·m (0.6 kg-m, 52
in-lb)
- Fit a dial indicator to the drive gear face to measure the backlash.
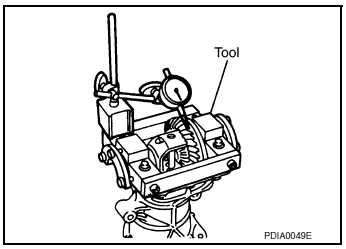
Standard
Backlash : Refer to DLN-141, "Backlash".
- If the backlash is outside of the specified value, change the
thickness of side bearing adjusting shims.
When the backlash is large:
Make drive gear back adjusting shims thicker, and drive
gear front adjusting shims thinner. For selecting adjusting
shim, refer to the latest parts information.
When the backlash is small:
Make drive gear back adjusting shims thinner, and
drive gear front adjusting shims thicker. For selecting
adjusting shim, refer to the latest parts information.
Inspection
INSPECTION AFTER DISASSEMBLY
Drive Gear and Drive Pinion
- Clean up the disassembled parts.
- If the gear teeth never mesh or line-up correctly, determine the
cause and adjust or replace as necessary.
- If the gears are worn, cracked, damaged, pitted or chipped (by
friction) noticeably, replace with new drive
gear and drive pinion as a set.
Bearing
- Clean up the disassembled parts.
- If any chipped (by friction), pitted, worn, rusted or scratched
marks, or unusual noise from the bearing is
observed, replace as a bearing assembly (as a new set).
Oil Seal
- Whenever disassembled, replace.
- If wear, deterioration of adherence (sealing force lips), or
damage is detected on the lips, replace them.
Differential Assembly
DIFFERENTIAL CASE
- Clean up the disassembled parts.
- If any wear or crack on the contact sides of the differential case
is found, replace.
SIDE GEAR AND PINION MATE GEAR
- Clean up the disassembled parts.
- If any cracks or damage on the surface of the tooth is found,
replace.
- If any worn or chipped mark on the contact sides of the thrust
washer is found, replace.
SIDE GEAR THRUST WASHER AND PINION MATE THRUST WASHER
- Clean up the disassembled parts.
- If it is chipped (by friction), damaged, or unusually worn,
replace.
DRIVE PINION
Exploded View
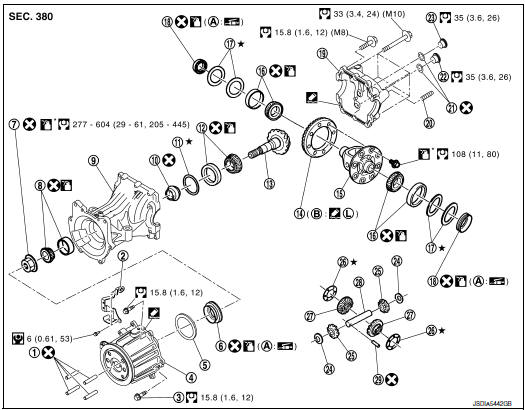
- Stud bolt
- Connector bracket
- Reamer bolt
- Electric controlled coupling assembly
- Wave spring
- Drive pinion oil seal
- Drive pinion lock nut
- Pinion front bearing
- Gear carrier
- Collapsible spacer
- Drive pinion adjusting shim
- Pinion rear bearing
- Drive pinion
- Drive gear
- Differential case
- Side bearing
- Side bearing adjusting shim
- Side oil seal
- Rear cover
- Stud bolt
- Gasket
- Drain plug
- Filler plug
- Pinion mate thrust washer
- Pinion mate gear
- Side gear thrust washer
- Side gear
- Pinion mate shaft
- Lock pin
- Oil seal lip
- Screw hole
: N·m (kg-m, in-lb)
: N·m (kg-m, ft-lb)
: Always replace after every
disassembly.
: Select with proper
thickness.
: Apply gear oil.
*: Apply anti-corrosion oil.
: Apply multi purpose grease.
: Apply Genuine Silicone RTV or
equivalent. Refer to GI-22, "Recommended Chemical Products and Sealants".
: Apply Genuine High Strength
Thread Locking Sealant or equivalent. Refer to GI-22, "Recommended Chemical
Products
Disassembly and Assembly
DISASSEMBLY
- Remove electric controlled coupling assembly. Refer to DLN-121,
"Disassembly and Assembly".
- Remove differential assembly. Refer to DLN-125, "Disassembly and
Assembly".
- Remove drive pinion oil seal, using oil seal remover (commercial
service tool).
- Fit drive pinion socket (A) onto drive pinion spline. Remove drive
pinion lock nut, using the pinion nut wrench (B).
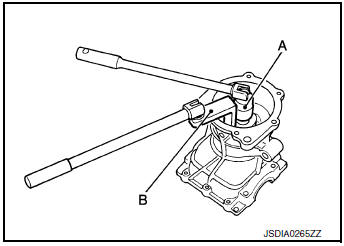
A : Drive pinion socket [SST: KV38109500 ( — )]
B : Pinion nut wrench [SST: KV38109400 ( — )]
- Press drive pinion assembly out of gear carrier.
CAUTION:
Never drop drive pinion assembly.
- Remove pinion front bearing inner race.
- Remove collapsible spacer.
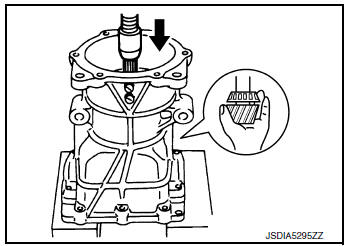
- Remove pinion rear bearing inner race from drive pinion, using
the separator (A) and the puller (B).
A : Separator (commercial service tool)
B : Puller (commercial service tool)
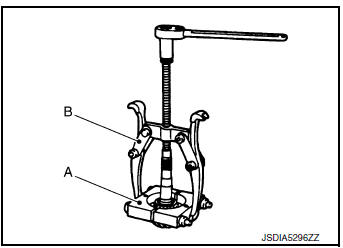
- Using a brass rod or equivalent (A), tap pinion front bearing
outer race evenly from the 2 cutouts on gear carrier and remove
pinion front bearing outer race.
CAUTION:
Be careful not to damage gear carrier.
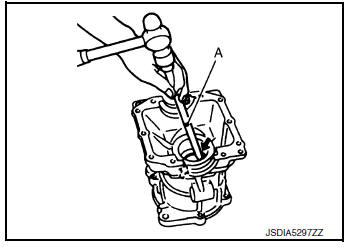
- Using a brass rod or equivalent (A), tap drive pinion adjusting
shim evenly from the 2 cutouts on gear carrier and remove drive
pinion adjusting shim and pinion rear bearing outer race.
CAUTION:
Be careful not to damage gear carrier.
- Perform inspection after disassembly. Refer to DLN-140,
"Inspection".
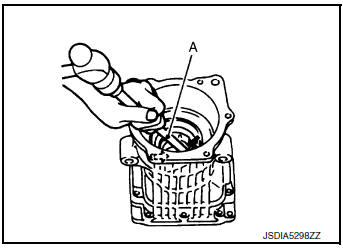
ASSEMBLY
- Install a drive pinion adjusting shim of the same thickness as
was installed prior to disassembly. Press pinion rear bearing
outer race into gear carrier, using the drift (A) [SST: ST17130000
( — )].
CAUTION:
- At first, using a hammer, tap bearing outer race until it
becomes flush to gear carrier.
- Never reuse pinion rear bearing outer race.
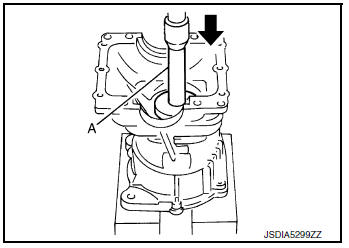
- Press pinion front bearing outer race into gear carrier, using the
drift (A) [SST: ST33230000 (J-25805-01)].
CAUTION:
- At first, using a hammer, tap bearing outer race until it
becomes flush to gear carrier.
- Never reuse pinion front bearing outer race.
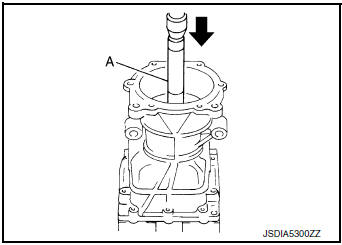
- Press pinion rear bearing inner race to drive pinion, using the
drift (A) [SST: ST23860000 ( — )].
CAUTION:
Never reuse pinion rear bearing inner race.
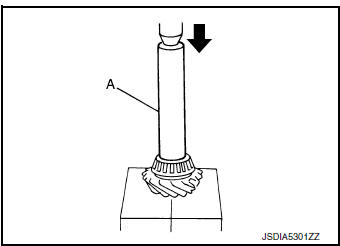
- Check and adjust the tooth contact and back lash of drive gear and drive
pinion following the procedure
below.
- Assemble drive pinion into gear carrier.
CAUTION:
- Never assemble collapsible spacer.
- Apply gear oil to pinion rear bearing.
- Assemble pinion front bearing inner race to drive pinion assembly.
CAUTION:
- Never reuse pinion front bearing inner race.
- Apply gear oil to pinion front bearing.
- Using the drifts (A and C) and press stand (B), press pinion front
bearing inner race to drive pinion as far as drive pinion lock nut
can be tightened.
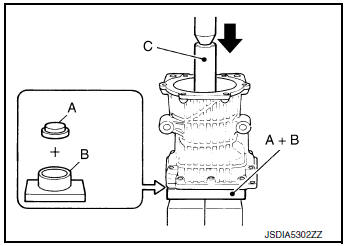
A : Drift [SST: KV40100610 (J-26089)]
B : Press stand [SST: ST38220000 ( — )]
C : Drift [SST: ST23860000 ( — )]
- Temporarily tighten removed drive pinion lock nut to drive pinion.
NOTE:
Use removed drive pinion lock nut only for the preload measurement.
- Rotate drive pinion more than 20 times to adjust bearing.
- Fit the drive pinion socket (A) onto the drive pinion. Using the
pinion nut wrench (B), tighten drive pinion lock nut holding drive
pinion, while adjusting pinion bearing preload torque using preload
gauge (C).
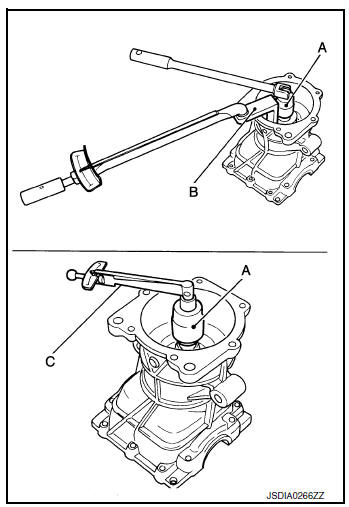
A: Drive pinion socket [SST: KV38109500 ( — )]
B : Pinion nut wrench [SST: KV38109400 ( — )]
C : Preload gauge [SST: ST3127S000 (J-25765-A)]
Pinion bearing preload : Refer to DLN-141, "Preload
Torque".
CAUTION:
Drive pinion lock nut is tightened with no collapsible
spacer. Be careful not to overtighten it. While measuring the
preload, tighten it by 5° to 10°.
- Install new side bearing adjusting shims (2 pieces for one side) with
the same thickness or re-install the
old ones to the same mounting position they were in prior to disassembly.
Install differential assembly to
gear carrier. Refer to DLN-125, "Disassembly and Assembly".
CAUTION:
Apply differential gear oil to the side bearings.
- Check and adjust tooth contact, drive gear to drive pinion
backlash. Refer to DLN-130, "Adjustment".
- Remove differential assembly.
- Remove drive pinion assembly from gear carrier
- Remove drive pinion nut and press drive pinion assembly out of
gear carrier.
- Remove pinion front bearing inner race.
- Assemble collapsible spacer 1 to drive pinion 2.
CAUTION:
- Be careful of the mounting direction of collapsible spacer.
- Never reuse collapsible spacer.
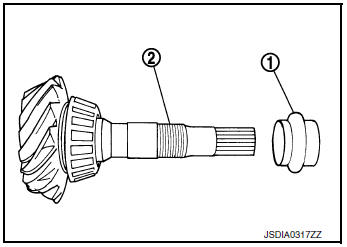
- Assemble drive pinion into gear carrier.
CAUTION:
Apply gear oil to pinion rear bearing.
- Assemble pinion front bearing inner race to drive pinion assembly.
CAUTION:
- Never reuse pinion front bearing inner race.
- Apply gear oil to pinion front bearing.
- Using the drifts (A and C) and press stand (B), press pinion front
bearing inner race to drive pinion as far as drive pinion lock nut
can be tightened.
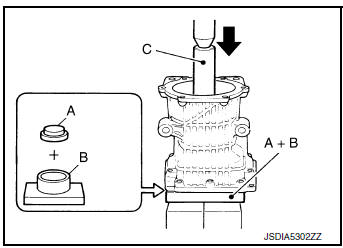
A : Drift [SST: KV40100610 (J-26089)]
B : Press stand [SST: ST38220000 ( — )]
C : Drift [SST: ST23860000 ( — )]
- Apply anti-corrosion oil to the thread and seat of drive pinion
lock nut, and temporarily tighten drive pinion lock nut to drive
pinion.
CAUTION:
Never reuse drive pinion lock nut.
- Fit the drive pinion socket (A) onto the drive pinion. While
holding
drive pinion, tighten drive pinion lock nut within the limits of
specified torque so as to keep the pinion bearing preload within
a standard values, using the pinion nut wrench (B) and the preload
gauge (C).
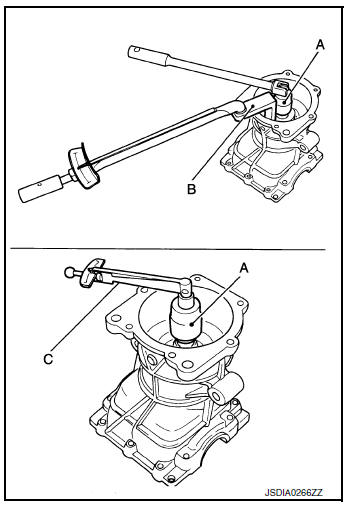
A : Drive pinion socket [SST: KV38109500 ( — )]
B : Pinion nut wrench [SST: KV38109400 ( — )]
C : Preload gauge [SST: ST3127S000 (J-25765-A)]
Drive pinion lock nut
tightening torque
: Refer to DLN-135, "Exploded
View".
Pinion bearing preload : Refer to DLN-141, "Preload
Torque".
CAUTION:
- Adjust the lower limit of the drive pinion lock nut tightening
torque first.
- If the preload torque exceeds the specified value, replace
collapsible spacer and tighten it again to adjust. Never
loose n drive pinion lock nut to adjust the preload torque.
- After adjustment, rotate drive pinion back and forth 2 to 3
times to check for unusual noise, rotation malfunction,
and other malfunctions.
- Install differential assembly. Refer to DLN-125, "Disassembly and
Assembly".
CAUTION:
Never install rear cover at this timing.
- Check and adjust drive gear runout, tooth contact, and drive gear to
drive pinion backlash. Refer to DLN-
130, "Adjustment".
- Remove dummy cover set [SST: KV381086S1 ( — )], then install rear
cover, and side oil seal. Refer to
DLN-125, "Disassembly and Assembly".
- Check total preload torque. Refer to DLN-130, "Adjustment".
- Using the drift (A) [SST: ST35271000 (J-26091)], install drive
pinion oil seal 1 within the dimension (D) shown as follows.
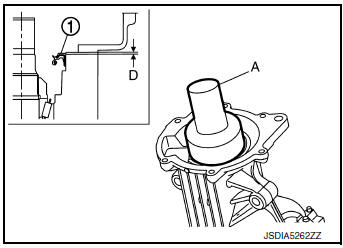
D : 0.8 – 1.2 mm (0.031 – 0.047 in)
CAUTION:
- Never reuse oil seal.
- When installing, never incline oil seal.
- Apply multi-purpose grease onto oil seal lips, and gear oil
onto the circumference of oil seal.
- Install electric controlled coupling assembly. Refer to DLN-121,
"Disassembly and Assembly".
Inspection
INSPECTION AFTER DISASSEMBLY
Drive Gear and Drive Pinion
- Clean up the disassembled parts.
- If the gear teeth never mesh or line-up correctly, determine the
cause and adjust or replace as necessary.
- If the gears are worn, cracked, damaged, pitted or chipped (by
friction) noticeably, replace with new drive
gear and drive pinion as a set.
Bearing
- Clean up the disassembled parts.
- If any chipped (by friction), pitted, worn, rusted or scratched
marks, or unusual noise from the bearing is
observed, replace as a bearing assembly (as a new set).
Oil Seal
- Whenever disassembled, replace.
- If wear, deterioration of adherence (sealing force lips), or
damage is detected on the lips, replace them.
REAR FINAL DRIVE ASSEMBLY
Exploded View
Final drive mounting bracket
Mounting stopper
Rear final drive assembly
: N·m (kg-m, ft-lb)
: Always replace after every
disassembly.
Rem ...
General Specifications
Preload Torque
Drive Gear Runout
Backlash
Differential Side Gear Clearance
...
Other materials:
Front regulator
Exploded View
Front door panel
Front door regulator
Front door power window motor
Front door glass run rear
Front door glass run front
Front door glass
Front door glass rubber run
Removal and Installation
REMOVAL
Remove the front door finisher. Refer to INT-15, ...
Monitor, climate, audio, phone and voice recognition systems
WARNING
Positioning of the heating or air conditioning
controls and display controls
should not be done while driving in order
that full attention may be given to
the driving operation.
Do not disassemble or modify this system.
If you do, it may result ...
FM/AM/SAT radio with compact disc (CD) player (Type A) (if so equipped)
FM/AM/SAT radio with compact disc (CD) player (Type A)
CD eject button
XM button*
Display screen
CD insert slot
SEEK button
SCAN button
CAT button
BACK button
APPS button
ENTER/SETTING button/ TUNE/SCROLL
knob
&n ...
© 2014-2025 Copyright www.nirogue.com