Nissan Rogue Service Manual: Front disc brake
BRAKE CALIPER ASSEMBLY (1 PISTON TYPE)
BRAKE CALIPER ASSEMBLY (1 PISTON TYPE) : Exploded View
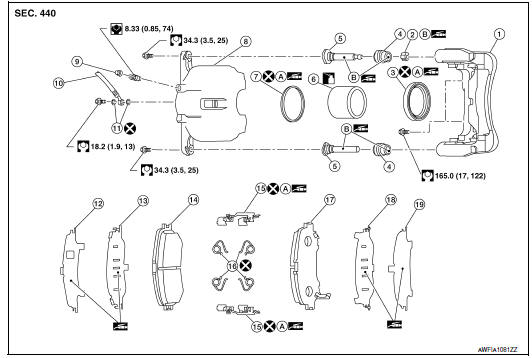
- Torque member
- Bushing
- Piston boot
- Slide pin boot
- Slide pin
- Piston
- Piston seal
- Brake caliper body
- Bleeder cap
- Brake hose
- Copper sealing washers
- Inner shim cover
- Inner shim
- Inner pad
- Pad retainer
- Anti-rattle clip
- Outer pad
- Outer shim
- Outer shim cover
- Molykote AS-880N
- Niglube Rx-2
: Apply brake fluid.
BRAKE CALIPER ASSEMBLY (1 PISTON TYPE) : Disassembly and Assembly
DISASSEMBLY
- Remove the brake caliper from the vehicle. Refer to BR-35, "BRAKE
CALIPER ASSEMBLY (1 PISTON
TYPE) : Removal and Installation".
- Remove sliding pins and sliding pin boots from torque member.
- Place a wooden block in brake caliper body and blow air from
union bolt hole to remove piston and piston boots.
WARNING:
Do not get fingers caught between piston and brake caliper
body.
CAUTION:
Do not reuse piston boots.
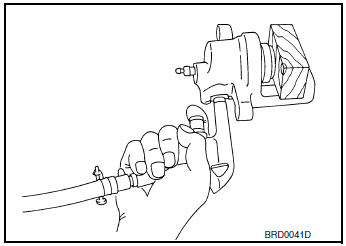
- Remove piston seals from brake caliper body using suitable tool.
CAUTION:
- Do not damage cylinder inner wall.
- Do not reuse piston seals.
- Remove bleeder valve and cap.
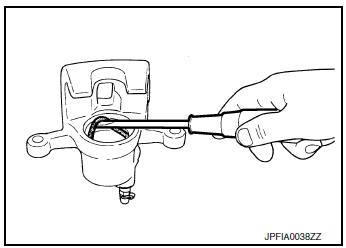
INSPECTION AFTER DISASSEMBLY
Brake Caliper Body
Check the inner wall of the brake caliper body for rust, wear, cracks or
damage. Replace the brake caliper
body if any abnormal condition is detected.
CAUTION:
Always clean with new brake fluid. Do not clean with mineral oil such as
gasoline and light oil.
Torque Member
Check the torque member for rust, wear, cracks or damage. Replace the torque
member if any abnormal condition
is detected.
Piston
Check the surface of the piston for rust, wear, cracks or damage. Replace the
piston if any abnormal condition
is detected.
CAUTION:
Piston sliding surface is plated. Do not polish with sandpaper.
Sliding Pin and Sliding Pin Boot
Check the sliding pins and sliding pin boots for rust, wear, cracks or
damage. Replace the parts if any abnormal
condition is detected.
ASSEMBLY
- Install bleeder valve and cap.
- Apply rubber grease to each piston seal (1), and install them to
the brake caliper body.
CAUTION:
Do not reuse piston seal.
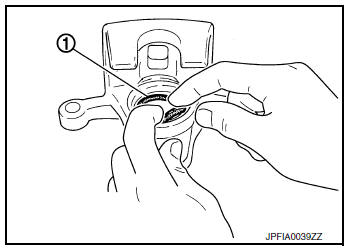
- Apply rubber grease to the piston boots. Cover each piston end
with a piston boot, and then install cylinder side lip on piston
boot securely into a groove on brake caliper body.
CAUTION:
Do not reuse piston boots.
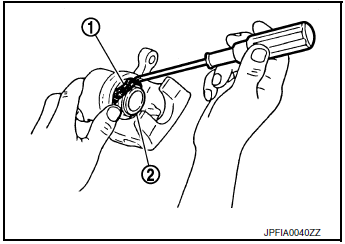
- Apply brake fluid to each piston (1). Push each piston into cylinder
body by hand and push piston boot (2) piston-side lip into
the piston groove.
CAUTION:
Press the piston evenly and vary the pressing point to prevent
cylinder inner wall from being rubbed.
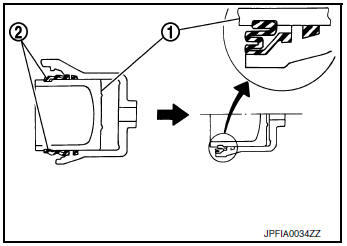
- Apply rubber grease to bushing; install bushing to sliding pin.
- Apply rubber grease to sliding pins and sliding pin boots, install
sliding pins and sliding pin boots to torque
member.
- Install the brake caliper to the vehicle. Refer to BR-35, "BRAKE
CALIPER ASSEMBLY (1 PISTON TYPE)
: Removal and Installation".
INSPECTION AFTER INSTALLATION
- Check the drag of front disc brake. If any drag is found, follow
the procedure described below.
- Remove brake pads.
- Using a suitable tool, press the piston into the brake caliper
body.
CAUTION:
Do not damage the piston boots.
- Install brake pads.
- Depress the brake pedal several times.
- Check the drag of front disc brake again. If any drag is found,
disassemble the brake caliper body.
- Burnish contact surfaces after refinishing or replacing disc
rotors or if a soft pedal occurs at very low mileage.
Refer to BR-18, "Brake Burnishing".
BRAKE CALIPER ASSEMBLY (2 PISTON TYPE)
BRAKE CALIPER ASSEMBLY (2 PISTON TYPE) : Exploded View
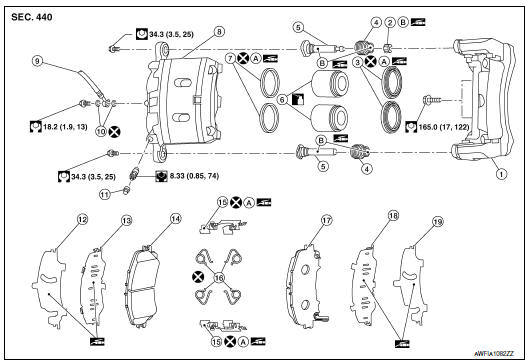
- Torque member
- Bushing
- Piston boot
- Slide pin boot
- Slide pin
- Piston
- Piston seal
- Brake caliper body
- Bleeder cap
- Brake hose
- Copper sealing washers
- Inner shim cover
- Inner shim
- Inner pad
- Pad retainer
- Anti-rattle clip
- Outer pad
- Outer shim
- Outer shim cover
- Molykote AS-880N
- Niglube Rx-2
: Apply brake fluid.
BRAKE CALIPER ASSEMBLY (2 PISTON TYPE) : Disassembly and Assembly
DISASSEMBLY
- Remove the brake caliper from the vehicle. Refer to BR-39, "BRAKE
CALIPER ASSEMBLY (2 PISTON
TYPE) : Removal and Installation".
- Remove sliding pins and sliding pin boots from torque member.
- Place a wooden block in brake caliper body and blow air from
union bolt hole to remove pistons and piston boots.
WARNING:
Do not get fingers caught between pistons and brake caliper
body.
CAUTION:
Do not reuse piston boots.
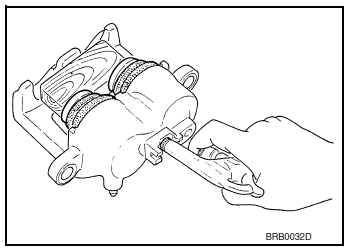
- Remove piston seals from brake caliper body using suitable tool.
CAUTION:
- Do not damage cylinder inner wall.
- Do not reuse piston seals.
- Remove bleeder valve and cap.
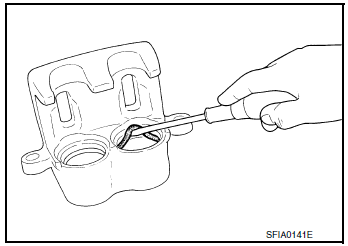
INSPECTION AFTER DISASSEMBLY
Brake Caliper Body
Check the inner wall of the brake caliper body for rust, wear, cracks or
damage. Replace the brake caliper
body if any abnormal condition is detected.
CAUTION:
Always clean with new brake fluid. Do not clean with mineral oil such as
gasoline and light oil.
Torque Member
Check the torque member for rust, wear, cracks or damage. Replace the torque
member if any abnormal condition
is detected.
Piston
Check the surface of the piston for rust, wear, cracks or damage. Replace the
piston if any abnormal condition
is detected.
CAUTION:
Piston sliding surface is plated. Do not polish with sandpaper.
Sliding Pin and Sliding Pin Boot
Check the sliding pins and sliding pin boots for rust, wear, cracks or
damage. Replace the parts if any abnormal
condition is detected.
ASSEMBLY
- Install bleeder valve and cap.
- Apply rubber grease to each piston seal (1), and install them to
the brake caliper body.
CAUTION:
Do not reuse piston seal.
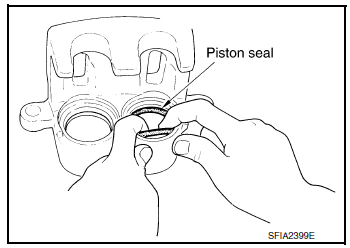
- Apply rubber grease to the piston boots. Cover each piston end
with a piston boot, and then install cylinder side lip on piston
boot securely into a groove on brake caliper body.
CAUTION:
Do not reuse piston boots.
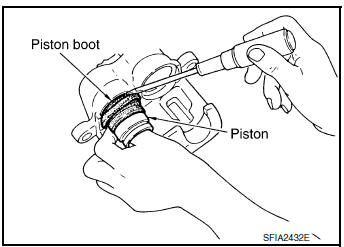
- Apply brake fluid to each piston (1). Push each piston into cylinder
body by hand and push piston boot (2) piston-side lip into
the piston groove.
CAUTION:
Press the piston evenly and vary the pressing point to prevent
cylinder inner wall from being rubbed.
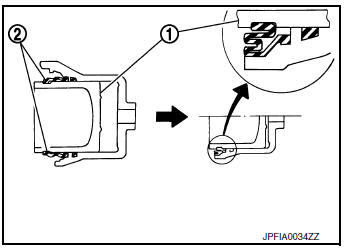
- Apply rubber grease to bushing; install bushing to sliding pin.
- Apply rubber grease to sliding pins and sliding pin boots, install
sliding pins and sliding pin boots to torque
member.
- Install the brake caliper to the vehicle. Refer to BR-39, "BRAKE
CALIPER ASSEMBLY (2 PISTON TYPE)
: Removal and Installation".
INSPECTION AFTER INSTALLATION
- Check the drag of front disc brake. If any drag is found, follow
the procedure described below.
- Remove brake pads.
- Using a suitable tool, press the pistons into the brake caliper
body.
CAUTION:
Do not damage the piston boots.
- Install brake pads.
- Depress the brake pedal several times
- Check the drag of front disc brake again. If any drag is found,
disassemble the brake caliper body.
- Burnish contact surfaces after refinishing or replacing disc
rotors or if a soft pedal occurs at very low mileage.
Refer to BR-18, "Brake Burnishing".
Exploded View
Sliding pin bolt
Sliding pin bolt bushing
Cap
Bleeder valve
Brake caliper body
Piston seal
Piston
Piston boot
Sliding pin boot
&nb ...
Other materials:
General maintenance
During the normal day-to-day operation of the
vehicle, general maintenance should be performed
regularly as prescribed in this section. If
you detect any unusual sounds, vibrations or
smells, be sure to check for the cause or have a
NISSAN dealer do it promptly. In addition, you
should notify ...
Glass lid
Exploded View
Panoramic roof glass
Glass lid
Side trim covers (LH/RH)
Front drain hose (LH/RH)
Moonroof motor assembly
Sunshade motor assembly
Moonroof front bracket (LH/RH)
Moonroof rear bracket (LH/RH)
Rear drain hose (LH/RH)
Moonroof unit assembly ...
U1000 CAN COMM circuit
Description
CAN (Controller Area Network) is a serial communication line for real-time
application. It is an on-vehicle multiplex
communication line with high data communication speed and excellent malfunction
detection ability.
Many electronic control units are equipped onto a vehicle, and ...
В© 2014-2025 Copyright www.nirogue.com